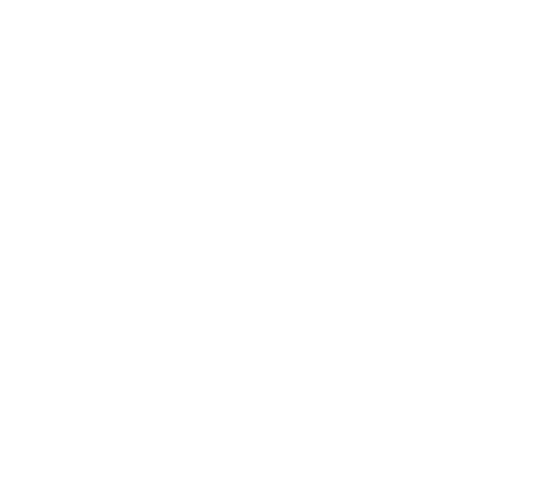
Using Multivariate Data Analysis in Predictive Process Control
My third and final blog in this series on digital transformation in the life sciences industry focuses on multivariate data analysis (MVDA), which is a set of statistical techniques that can help users comb through multiple parameters in a data set simultaneously to assess their interactions and impacts and identify patterns in behavior. The objective is to pinpoint those variables responsible for most of the variability and, in doing so, sift out the informational “noise” and focus on the relationship between the key contributors. This ability to discern patterns and the way in which different variables can influence those patterns makes MVDA an effective tool in the predictive process control toolbox.
Predictive process control is monitoring and adjusting processes based on performance. Model predictive control (MPC) is an optimal control technique in which the calculated control actions minimize a cost function for a constrained, dynamical system over a finite, receding horizon. MVDA uses techniques, such as principal component analysis (PCA), to transform multiple variables into a smaller set of uncorrelated variables (“principal components”). This simplifies the analysis by eliminating redundant or irrelevant variables and makes it easier to identify the complex interrelationships and dependencies that support the process.
Traditional univariate statistical techniques focus on monitoring one quality variable at a time. This makes them unsuitable for analyzing process data where variables show collinear behaviors, such as complex manufacturing processes. MVDA applies primary component analysis and projection to form a new set of latent variables and forge an enhanced understanding of process behavior. If the variables are highly correlated, the process can be defined by a reduced set of latent variables, a linear combination of the original variables.
The benefits of applying MVDA in predictive process control in the life science industry include:
Improved Accuracy:
MVDA allows for the simultaneous analysis of multiple variables, considering their interrelationships. By incorporating several variables into the analysis, MVDA provides a more comprehensive understanding of the process, leading to enhanced accuracy in predictive modeling. It helps capture complex interactions and dependencies that may be missed when analyzing variables individually.
Enhanced Predictive Models:
MVDA enables the development of sophisticated predictive models by leveraging the correlations between multiple variables. By including additional inputs, such as process parameters, environmental factors, and historical data, MVDA helps build more robust and accurate models. These models can then predict process behavior and outcomes more effectively.
Dimensionality Reduction:
In many industrial processes, numerous variables can impact the outcome. MVDA techniques, such as PCA, can reduce the dimensionality of the data by transforming the variables into a smaller set of uncorrelated variables called principal components. This reduction in dimensionality simplifies the analysis, enhances interpretability, and eliminates redundant or irrelevant variables, improving efficiency and computational performance.
Real-Time Monitoring and Control:
MVDA can be applied to real-time monitoring and control systems, allowing for early detection of process deviations or abnormalities. By continuously analyzing multivariate data, MVDA methods can detect patterns or trends indicating impending process issues. This proactive approach enables timely interventions and adjustments to maintain optimal process conditions, minimize downtime, and reduce the risk of product defects.
Process Optimization:
MVDA provides insights into the relationships between process variables, which can be leveraged for process optimization. By understanding how different variables interact and influence the process, operators can identify critical factors and set optimal operating conditions. This optimization can improve efficiency, reduce resource consumption, increase product quality, and minimize waste or rework.
Fault Detection and Diagnosis:
MVDA techniques effectively identify faults and diagnose the root causes in complex processes. By analyzing multiple variables simultaneously, MVDA can detect abnormal patterns or outliers that may indicate faults or malfunctions. It helps operators pinpoint the variables or combination of variables responsible for the deviation, facilitating quicker troubleshooting and corrective actions.
Multivariate data analysis offers the life sciences industry robust tools for handling and interpreting complex data sets. By enabling the integration and analysis of multiple variables simultaneously, MVA enhances research efficiency, improves decision-making, and accelerates advancements in areas such as drug development, genomics, and clinical trials. This ultimately contributes to more effective and personalized healthcare solutions. I see the value and key advantages that MVDA provides over traditional univariate statistical techniques, which focus on monitoring one quality variable at a time and are not robust enough to analyze complex manufacturing processes effectively.
Contact Arcadis to learn more about how MVDA is being used to enhance predictive quality control in life science facilities.